
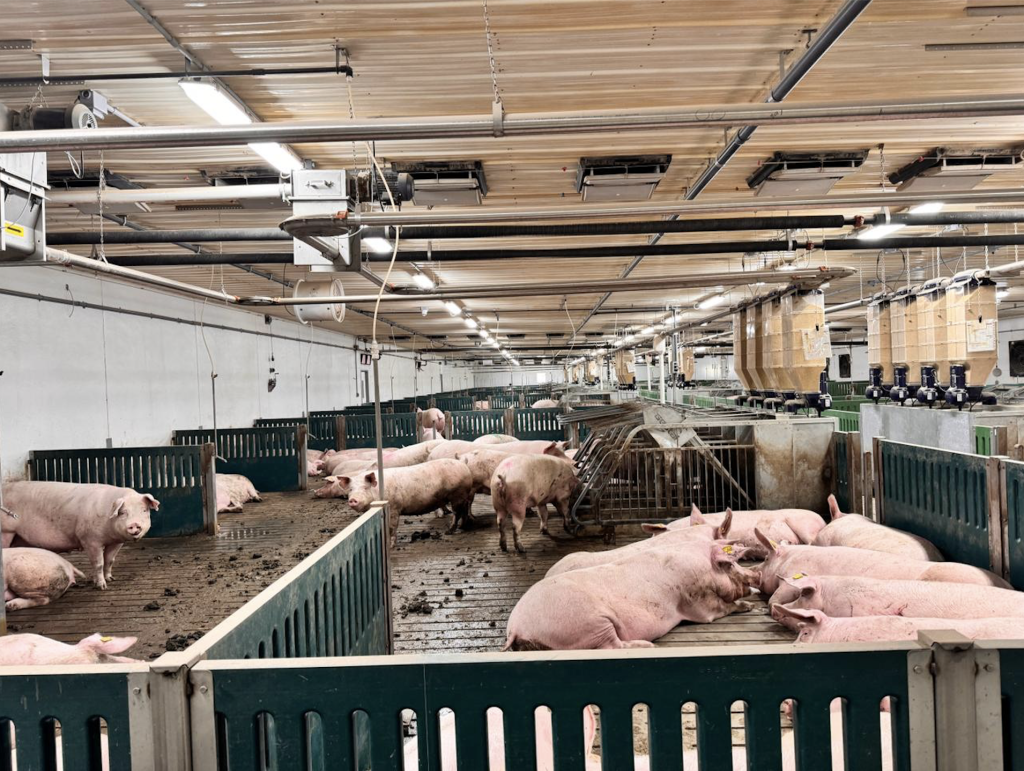
Lucas Maendel, the right hand to the hog boss at Blue Clay Colony near Arnaud, MB, shared his insights on their recently renovated group housing hog barn. Maendel highlighted the renovation’s efficiency and functionality, particularly how the barn’s layout design creates a seamless flow.
“It’s well set up,” Maendel noted, “describing the lack of obstructive alleyways or separate buildings, which allows for a smooth workflow.”
He emphasized that this renovation transformed a 30-year-old barn into a modern facility capable of housing 1,200 sows, proving the remodel was practical and highly effective.
The Canadian pork industry has developed its own Code of Practice to guide producers in the ethical and practical care of farm animals. Mark Fynn, Manitoba Pork’s Director of Animal Care and Quality Assurance, recently highlighted the upcoming requirements for group sow housing, a practice mandated by Canadian standards with a July 1, 2029 deadline. This transition requires producers to shift from traditional confinement methods to group housing, allowing sows to move more freely and encouraging natural behaviour.
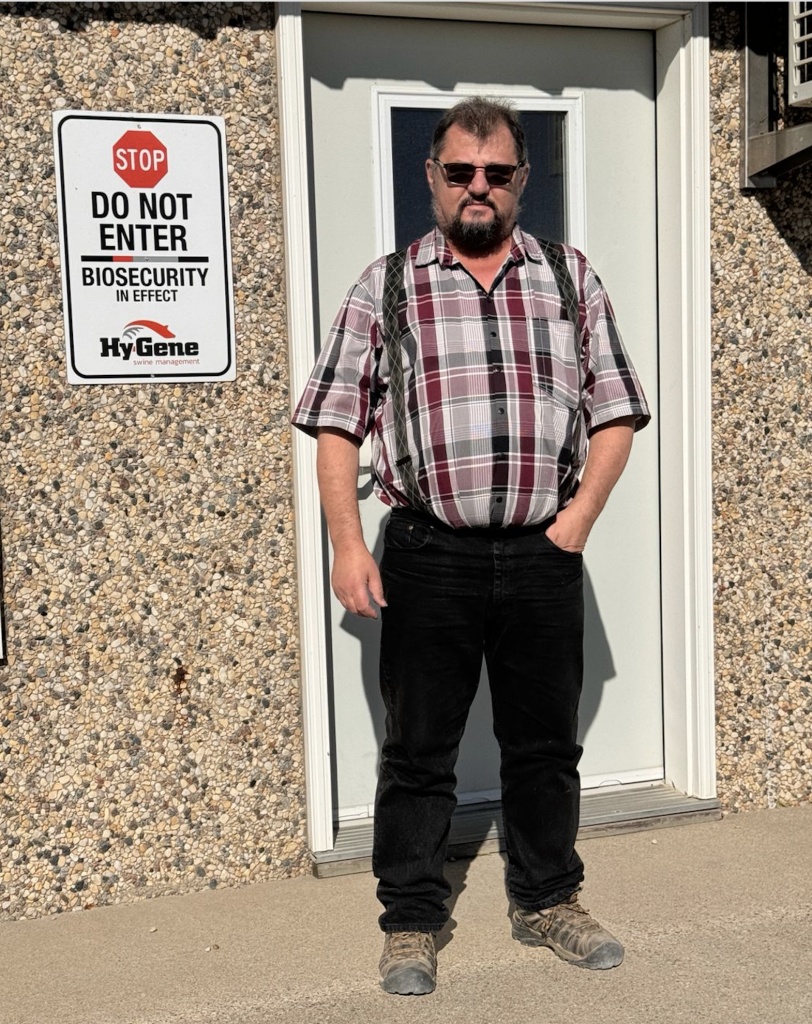
Larry Maendel began the recent tour with palpable pride, sharing, “We’re going to see a state-of-the-art, farrow-to-finish unit—everything.” The facility, fully equipped with the latest technology, is a modern marvel in hog production. “It’s the most advanced equipment and technology that the industry has to offer,” Larry notes, adding, “and it’s working awesome.”
This unit stands out not only for its cutting-edge features but also for its integration of smart technology. Maendel controls the ventilation remotely, allowing staff to monitor and adjust conditions directly from their phones. Larry points out that every system is set up to alert them with texts and calls for any irregularities—from feeding issues to low water pressure—ensuring prompt attention around the clock. While he admits, “It’s a bit annoying sometimes, especially at two or three a.m.,” he values the constant updates for the precision and control it brings. The unit accommodates around 1,200 farrow-to-finish sows, showcasing how far technology has transformed agricultural operations.
The hog boss of 30 years in the same colony enthusiastically explains the loose housing setup, calling it “a big step up from crates.” He shares, “I’d never go back. We love it.” Transitioning from traditional stalls to loose housing required adapting their management techniques, but he feels it’s been more than worth it. “There was a learning curve, but we’re in it now, and it’s going great,” he said.
Maendel highlights animal welfare when asked what makes the system so effective: “The hogs can choose where they want to go when they want to eat, and where to lie down. If one gets a bit aggressive, the others can move away.” He notes that any initial scrapping lasts only a few minutes, after which they relax. “You’ll see it when we walk through. They’re so calm they won’t even get up,” he adds, emphasizing how much the pigs benefit from the freedom and reduced stress in the new system.
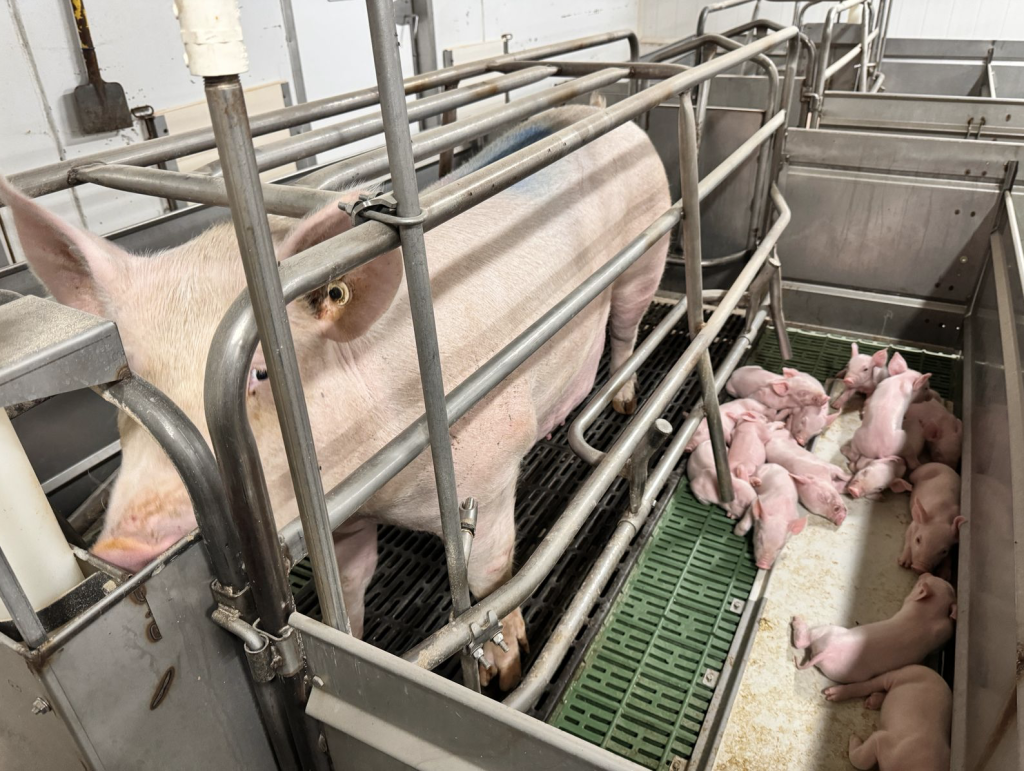
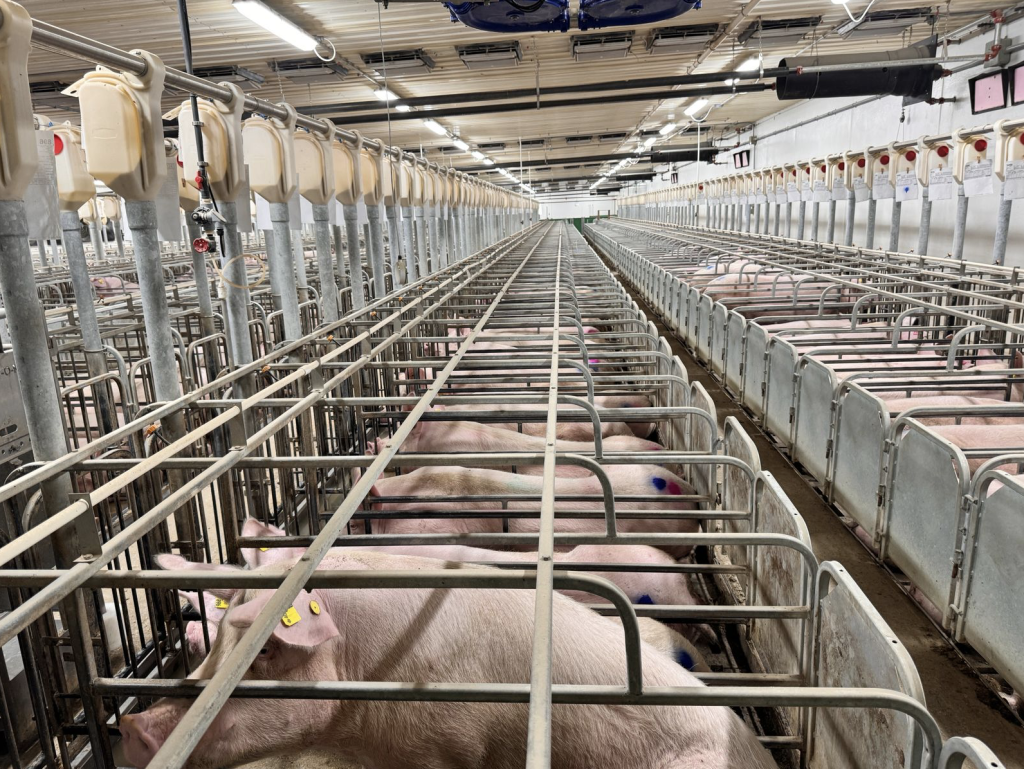
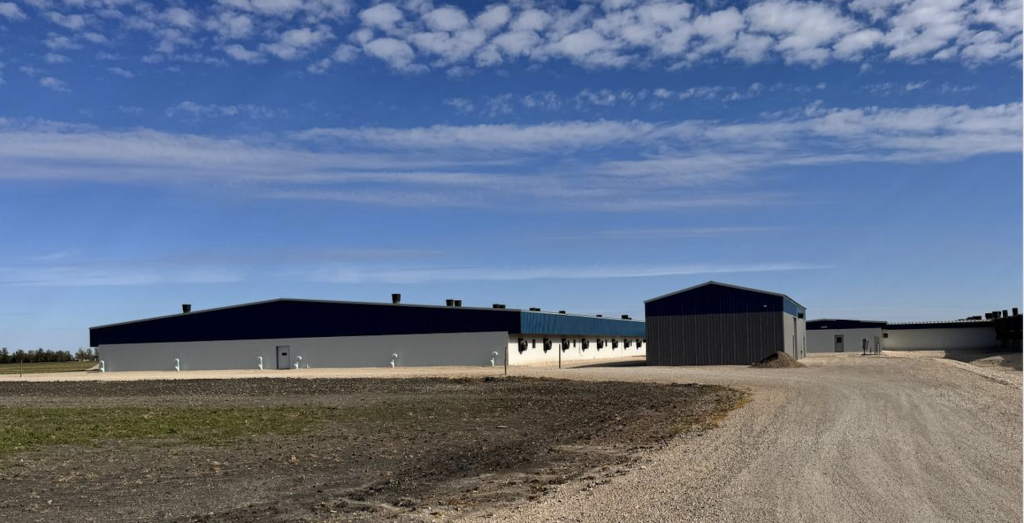
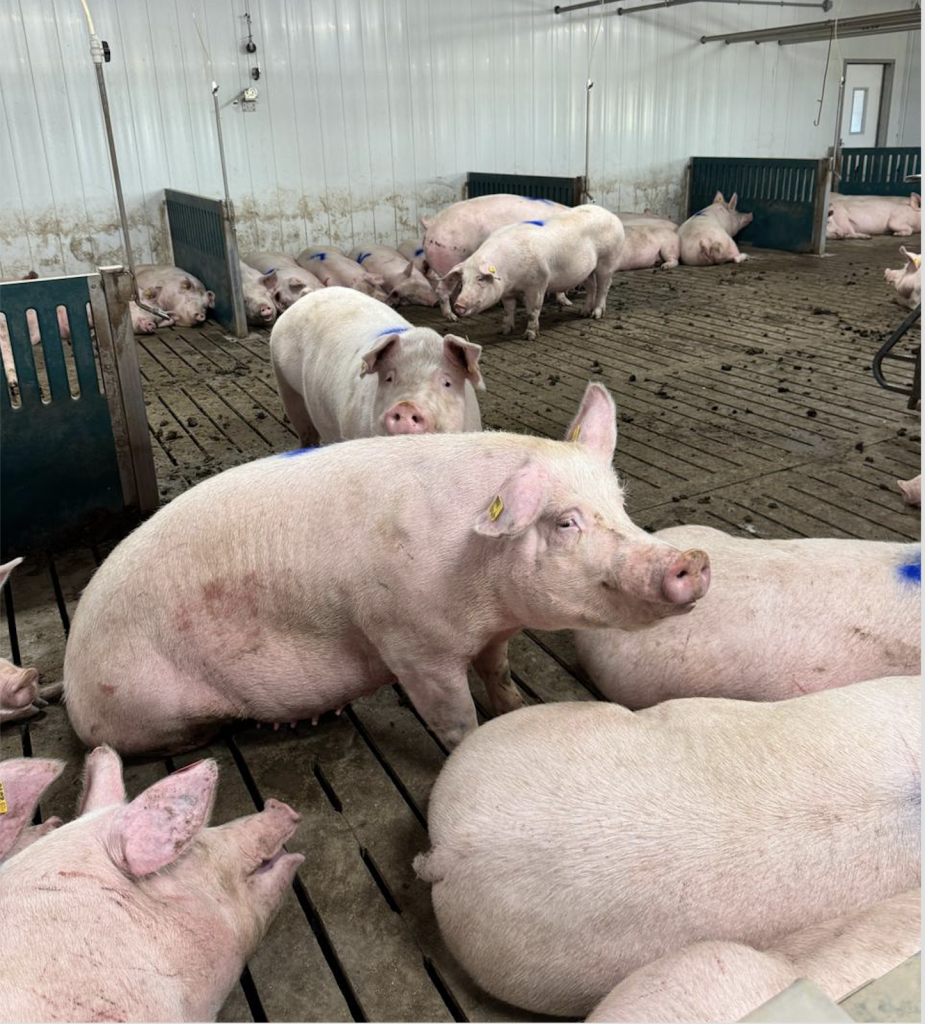
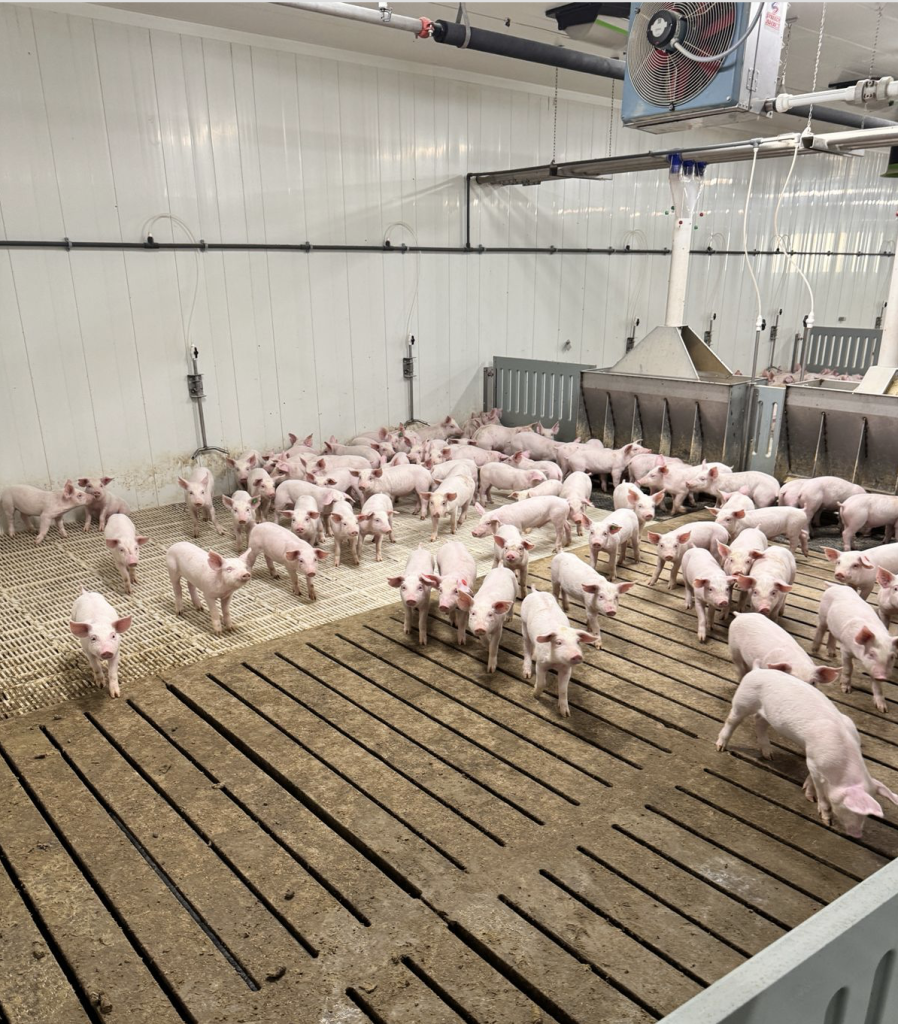
He speaks highly of Hypor genetics, sharing, “We love them.” He explains that Hypor has focused on loose housing for over 15 years, explicitly breeding out aggressiveness in their hogs to make them well-suited for this system. “Everything’s on camera,” he notes. “If they find an aggressive one, she’s culled. They think they’ve got it, and I feel they do because these animals aren’t aggressive at all.”
Maendel said group housing for pigs dramatically improves animal welfare by allowing them freedom of movement. “It’s cruel to lock them up their whole life,” he says. Although still adapting to the system as a young parity farm, Larry already sees “improved animal performance” in the new setup.
The farm’s decision to transition early aligns with industry regulations set for 2029. Rather than waiting, Larry’s team upgraded now, especially since their older barn needed repairs. “We’re glad we did. We’re miles ahead of other farms,” he shares, emphasizing that this proactive shift benefits animal welfare and positions the farm well for the future.
Each pen holds approximately 55 sows in the group housing area, with ten pens in the barn. The farrowing wing alone houses around 265 sows, and we can accommodate about 470 across the entire facility.
“Sows stay in each pen for 26 consecutive days, providing continuity in their care.”
Maendel said newly farrowed sows can sometimes be aggressive, particularly in group settings. However, the computerized system helps manage health and behavioural issues effectively, as it can identify sick animals through data tracking.
“We aim to wean 730 a week.” They maintain in-house genetics to ensure bio-security, producing their maternal lines and only bringing in semen to prevent bio-security risks.
“We’re at 31 pigs per sow annually,” Maendel said.
He attributes the success of their advanced operation to his dedicated team. “It’d be tough without good staff,” he says, praising his five employees for their skill and commitment. Larry notes that each team member works toward the farm’s goals and has the potential to become a great manager.
The facility incorporates durable materials—concrete, plastic, and stainless steel—designed for longevity and easy maintenance. “We wanted quality, so we invested in materials that would last,” Maendel says. The barn also features an efficient waste management system, collecting manure and channelling it to a pit beneath the building. This setup reflects their commitment to hygiene and reducing environmental impact. •
— By Harry Siemens
Harry was the recipient to a exclusive full barn tour on the Blue Clay hog operations, while following full bio security protocols (shower in & out), whilst his new wife spent time with the ladies in the kitchen. Thanks to Blue Clay for the personal tour.
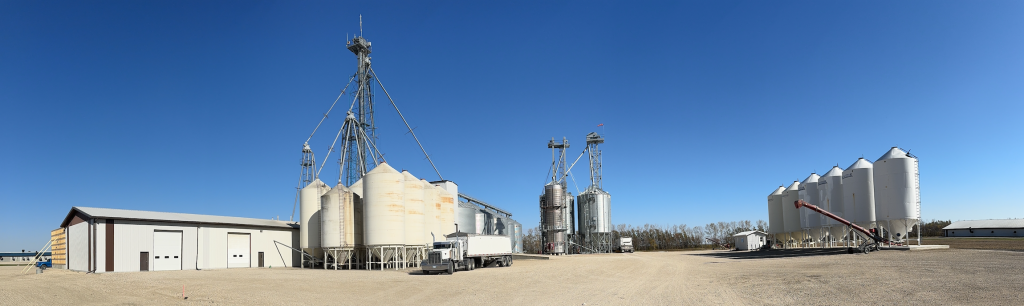