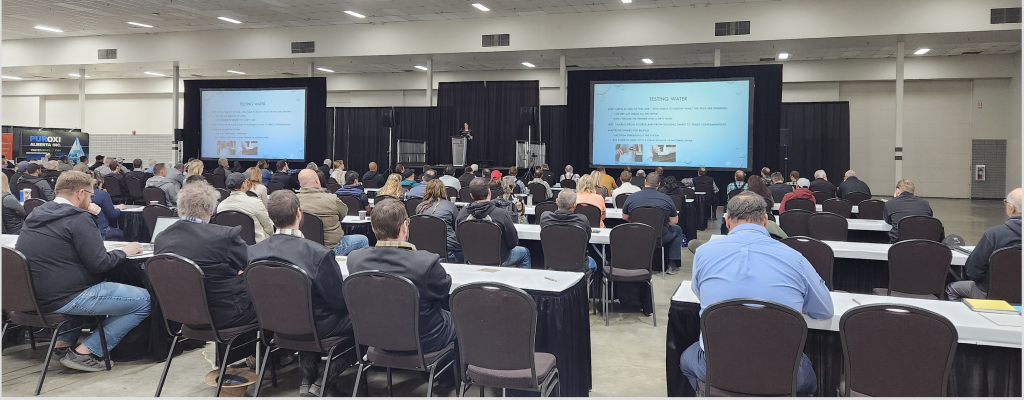
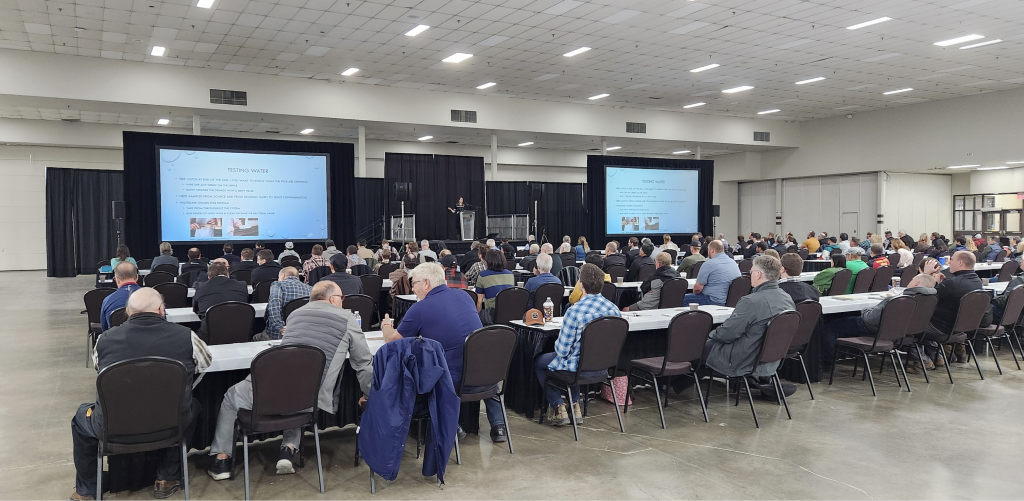
One constant in the evolving industry of swine production has been the annual Red Deer Swine Technology Workshop, created as a practical training session for producers, managers and barn staff. First hosted in 1999 by University of Alberta Professor Frank Aherne and nutritionist Jim Gowans, the RDSTW is now operated by a committee of volunteers working under Alberta Pork’s umbrella.
Their 25th edition, held at Westerner Park on October 9, attracted more than 200 registrants along with a strong contingent of sponsors who set up their exhibits around the perimeter.
“(The seminar) is aimed at producers and managers to get take-home messages and just take something back to the farm that you’re going to be able to use in a practical way to help improve your production and your knowledge,” Chair Alastair Bratton, Head of the Canadian pig division for Sunterra Farms said in opening the 2024 workshop.
RDSTW’s 25th edition brought together the varied expertise of individuals including veterinary consultant Luc Dufresne speaking about the impact of weaning age; a discussion around cleaning and maintaining water lines by veterinarian Hollyn Maloney, getting piglets off to a good start by producer Edwin Spruit and a frank talk about hiring temporary foreign workers by Trish Hyshka.
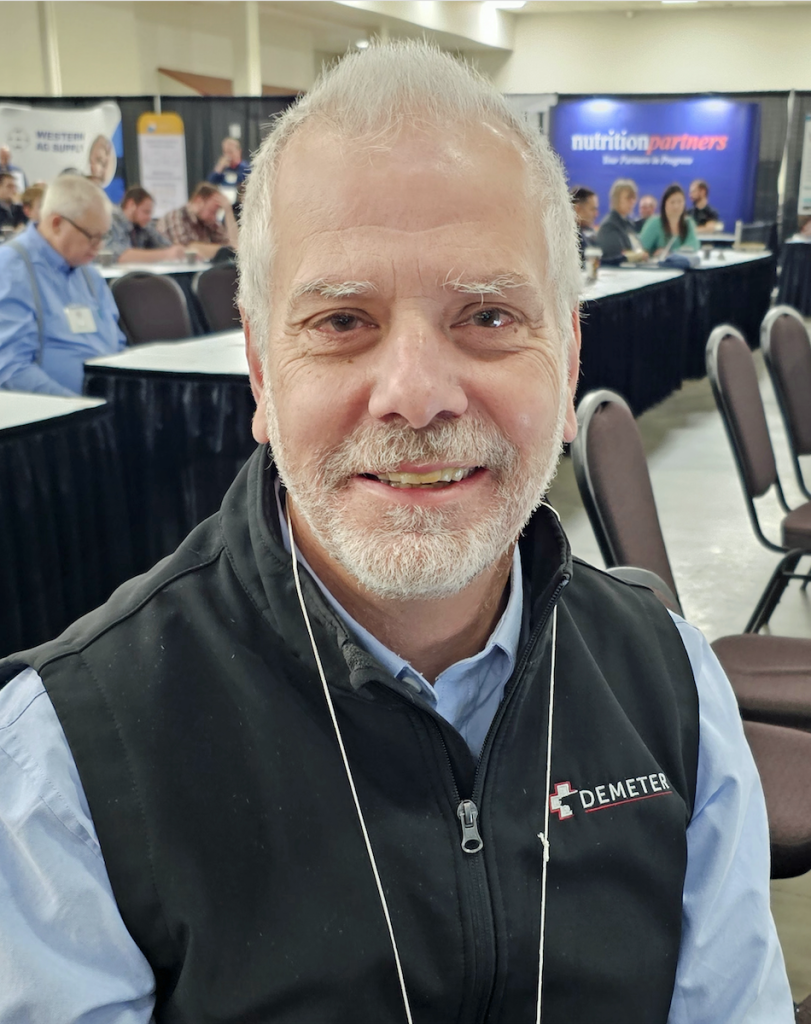
WHEN TO WEAN
Dufresne, who has returned to Quebec after a few years spent working in the United States, opened the workshop with his findings concerning the impact of early weaning and potential benefits of giving pigs a few more days on the sow.
“What makes sense and what is the impact as we fluctuate on the wean age aspect, and what does it do for pig performance, and overall, what’s the economic impact of those changes in Segregated Early Weaning?” said Dufresne.
In nature, sows gradually wean their pigs at around 11 to 15 weeks, he said. Commercial producers have shortened the amount of time their pigs spend on the sow. Early weaning evolved in the 1980s, aided in part by swine veterinarian Tony Alexander’s work on medicated early weaning to reduce pathogen exposure.
“He was able to eradicate specific disease by separating the pigs very early, at around seven to 10 days. That was actually a better process, an easier process than to C-section. After that, there’s been some significant improvement related to nutrition of the early piglets and development of and usage of more sophisticated ingredients that allow us to wean younger pigs and be able to feed them accurately,” said Dufresne.
“Those two changes basically made the rise of early weaning that was one of the major methods of production, and that was also at the time where intensive production really exploded in North America.”
Benefits of early weaning must be weighed against the costs that will affect the revenue potential from those pigs, said Dufresne.
“If we want to think about the impact of weaning age on the overall performance of the pigs, then most importantly, we have to look at the GI (gastro-intestinal) tract.”
The GI tract absorbs nutrients and plays a critical role in a pig’s immune system. Weaning pigs before that GI tract is fully developed will have a continuing and adverse affect on their health in the nursery and as they grow to maturity.
Dufresne offered data showing a balance can be determined by finding the optimum age for weaning pigs to manage costs and improve revenue. The added costs of keeping pigs back a few days longer can be seen in the improved performance including livability and weight gain, he said.
“A lot of the research has been done between 12 and 25 days of age. So, if we go outside of that, it’s getting a little bit trickier. We’ve got some data out 28 days that looks like it’s still looking like the linear response. Past that, it really looks like it’s tempering off,” he said.
Each management system will have its own considerations, including the amount of space available if the wean-service interval is to be extended, he said.
“The models showed that increasing the weaning age from 18 or 21 to 24 days improved crate efficiency and that crate capacity would increase both the farm total revenue (and) also the revenue per pig.
“More research is needed to determine the linear improvement in the economic benefit of increasing the wean age above 28 days.
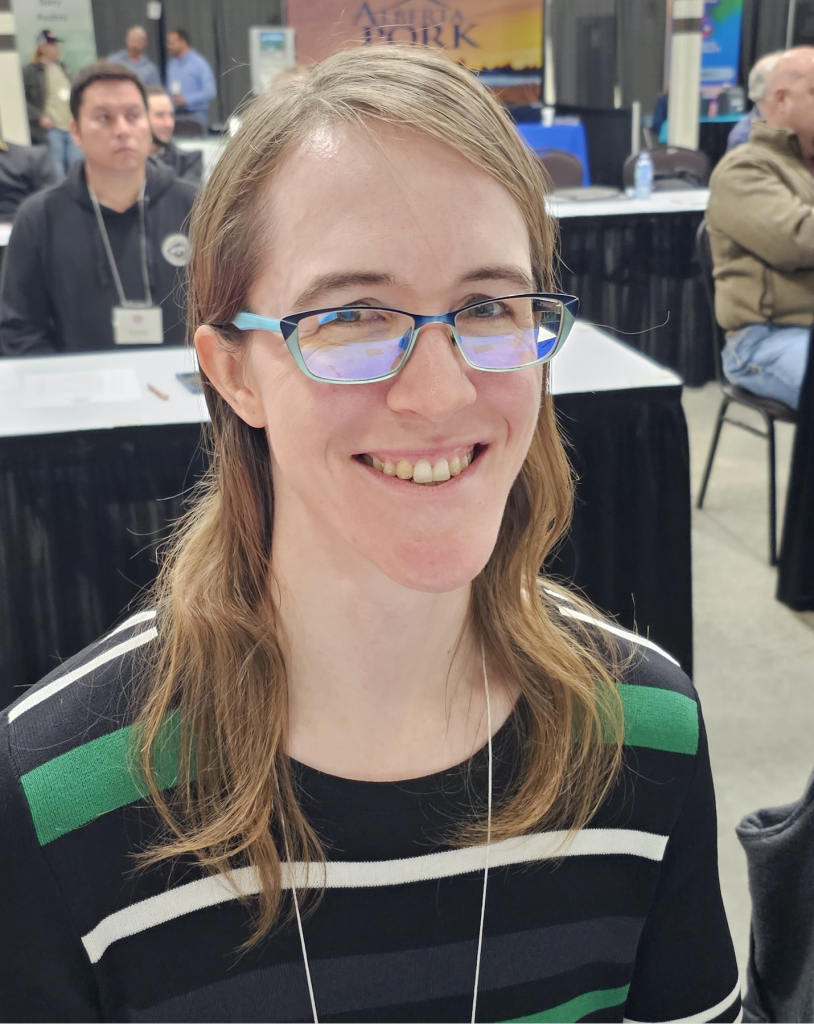
WATER PRIMER
Hollyn Maloney, a veterinarian with Alberta Agriculture and Irrigation, offered advice on sanitizing and maintaining water systems to help keep pigs healthy.
“Your pigs are taking a lot of feed, but they also drink a lot of water, and we don’t talk about it as much,” she said.
“When we’re estimating water consumption, we usually look at about 10 per cent of their body weight per day. Obviously, that’s going to vary a lot . . . depending on temperature. But it goes to show they’re drinking a lot of water. What else are they taking in when they’re drinking their water?”
Maloney emphasized the importance of regularly checking and cleaning water lines to control bacteria and other contaminants as well as temperature and fluidity.
Contaminants that effect water quality can enter the lines from the outlets as well as from the sources, she said. Biofilm is created by colonies of bacteria coating the line, and can contain funguses, viruses and other potential contaminants. Biofilm interferes with water flow and can slip into the water for the pigs to ingest.
“It produces a slime layer with different bacteria. They coat themselves in slime, which allows them to stick on and makes them really hard to get off. It also allows them to capture nutrients from the water, which allows them to thrive and grow, and so they survive better as this big old colony of bacteria and other microbes living together than they would just free floating in the water,” said Maloney.
Coliforms are an indicator of soil or manure contamination in the system, she said. Water testing generally looks at total coliforms, which should fall below 10 CFUs (colony-forming units) per 100 millilitres.
Clean samples should be taken from a free catch at the ends of the line as well as from the water sources and holding tanks. Swabs should be taken from inside the line to test for biofilm.
“Sponge with cleaning tweezers, just like you’d be scrubbing something in your barn, clean off the surface. You just scrub up the inside of the line somewhere and then there it is for culture and it will tell you all the different bacteria that are present and in what quantities and give you an idea if you’re starting to get an accumulation that could be causing problems.”
Flow rates will influence the number of bacteria growing in water lines, with stagnant water providing a good opportunity for bacteria to grow, said Maloney.
Checking flow rate can be accomplished easily, using the cap off a livestock marker. It should take about 12 seconds to fill in the nursery and six seconds in the rest of the system. Maloney recommends checking 10 per cent of the system every week.
A line that is starting to plug will back-flow, contributing to bacterial growth upstream, especially in areas like the flat bottom of a holding tank, where there is less flow under the outlet. In a warmer room, like a nursery, that stagnant water accelerates bacterial growth with the potential that the pig’s first drink delivers a load of pathogens, said Maloney.
She offered a number of recommendations for cleaning systems, with some cautions about which products are effective under different conditions.
For example, organic acids used to promote gut health also promote the growth of bacteria, while antibacterials will kill vaccines delivered through the water lines.
She advised using a sanitizer in the line when introducing organic acids. In Alberta, where well water is typically high in minerals, anti-scale products should be used to reduce lime, which contributes to the formation of biofilm. Any product used in the water lines must be food grade, as stated on the safety data sheet.
Peroxides are effective; hydrogen peroxide is generally safe for pigs in normal concentrations. However, some peroxides are “finicky” about pH and Alberta well water tends to be slightly basic. Maloney therefore recommends acidifying water to a pH between five and seven to allow proper performance of the chemical. She also advised that some sanitizers and descalers spoil quickly if left open at room temperature, so it is important to store them properly as stated on the label.
Maloney said the three steps most important for clean water are to perform regular bacterial swabs, sanitize and run the water to keep it clean.
If chlorine products are being used, it is important to allow contact time before flushing, she said. “You don’t just want chlorine going in and then going directly to your pig system. (It needs) to have enough time to kill the holding tank and then flow out.”
Maintaining clean water lines is the same thing as cleaning the barn, said Maloney.
“You’re just getting rid of biofilms off of your surfaces within your barns. You can’t actually get in there and scrub it out, so breaking down those organisms that are in there and breaking down that slime component with degreasers are your best bet,” she said.
A “massive” degrease once a year will do the job, provided there is not a lot of scale. She described additional steps involved in charging the lines and letting them soak, followed up with a flush.
She reminded producers to check safety data sheets and make sure products that could remain in the system are labelled for human or animal use.
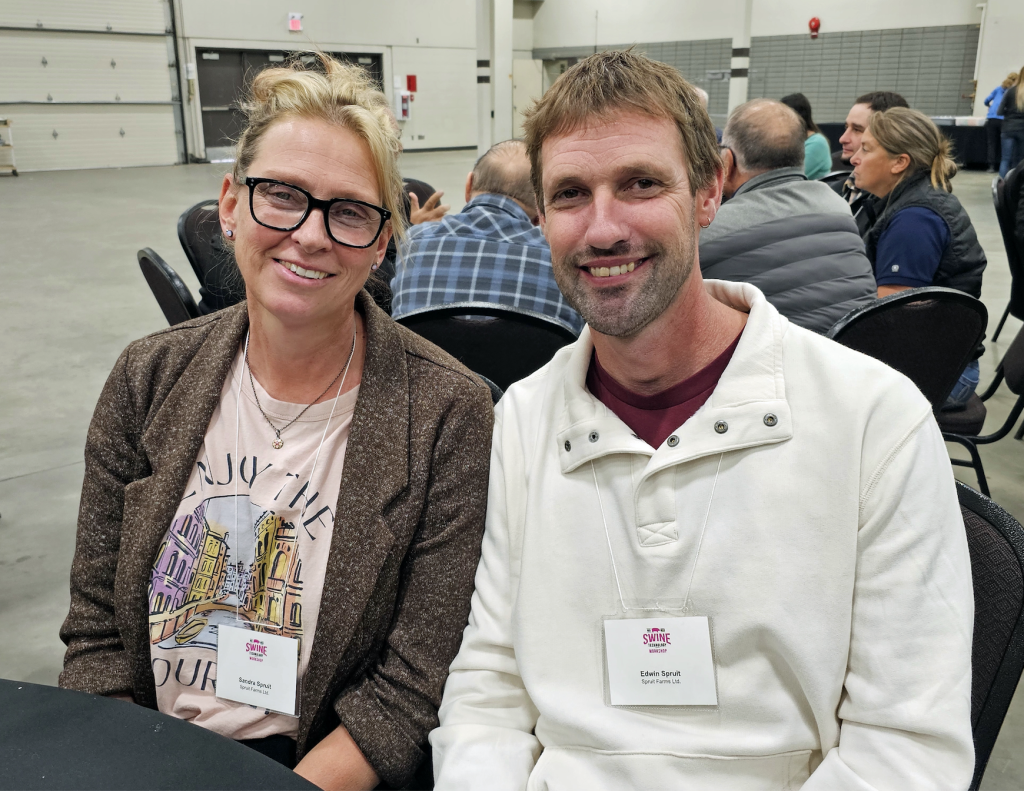
THE FIRST 48 HOURS
Producer Edwin Spruit from Red Deer County picked up the discussion with his thoughts on getting new pigs off to a good start.
The first step, he said, is to make sure vaccinations are up to date, including Rota A and Rota C as well as e. coli.
“We were always experiencing scours in our farrowing rooms, so we started researching, finding out what exactly the deal was. At that point, we were just vaccinating for e. coli. Right now, we’re vaccinating for Rota A and Rota virus C, and still the E coli. This made a difference in our occurrence of these scours. We still had enough scours going through, but it just didn’t last as long.”
Spruit said the vaccinations improved survivability because they reduced the impact of scours on the pigs.
“The other thing we started really looking at is the condition of the sows. We use the caliper once in a while, but the major thing is just to go around and make sure that those sows in the loose housing are actually getting the right amount of feed that they should get and that we don’t have those skinny or fat sows going in to farrowing.”
Spruit weans once a week, loading his farrowing rooms on Thursday for farrowing on the following Monday.
He ensures that each farrowing house is thoroughly cleaned between batches, including a scrub with cold water and detergent. The additional expense of using hot water does not pay off. The room is allowed to dry thoroughly after the wash, and then disinfected the next day.
Having enough spaces to accommodate his all-in-all-out system, Spruit said he never has to get in a hurry between batches, so it’s quite relaxed with no need to push the animals.
“Once we wean again, we’re not in a rush to load those houses,” he said.Farrowing rooms are held at 23C until about eight days after farrowing, then reduced to 18C to let the sows cool down. Rubber heat mats are provided to give the piglets a warm place to sleep.
Check sheets are placed on the door of each room to keep track of vaccinations and maintenance procedures, including checking and cleaning of water lines, said Spruit. Water nipples are checked at every round to make sure all of the stock are getting what they need to drink.
Spruit’s sows farrow in ordinary iron crates, supplied with rubber mats and heat lamps, towels and plenty of drying powder.
“We use quite a bit of it because . . . a fair portion of our piglets do get scours. So, we make sure every room has its own bottle.”
Spruit emphasized the importance of internal bio-security during the first 10 days of lactation. People working in the farrowing room change their boots at the door during that period, when the risk of infection is still high.
“We do put powder on the mat, but we also go around twice a day just to throw powder everywhere. We don’t dry the piglets with powder, it just becomes too much work to do. So, we just basically dry them off with the towels.”
He split suckles every litter that produces more than 12 pigs.
“We pull off the big piglets, the ones that have been the earlier born, the bigger, the full bellies and pull them off for half an hour to 45 minutes. We try to do it multiple times before we foster the big ones off, or the small ones, depending on what’s happening.”
Although fostering on the first day is not recommended, Spruit said he has had success with taking the biggest pigs off at the end of the first day.
“Our average is 15 per sow, so there’s multiple bigger litters. Leaving more than the amount of teats plus two gives us more mortality in the first night, so every time we count the number of teats on the sow, we count first, and if the sow has 16 teats, we leave no more than 18 piglets on that sow overnight. The rest get fostered off right away.”
Those big pigs are on the mom for 16 to 28 hours, while the rest of the pigs stay with her until weaning.
Piglets are processed at day two or day three, including vaccinations. Some will fall back after processing and Spruit at one time had a policy of letting them die if they were not going to thrive. However, that was quite difficult for the people working with the piglets, so he came up with an alternative.
His solution now is to place a bowl containing about 200 ml of milk in with them, and if they drain that, they get more.
“At the end of the day, if they did not drink that milk, they’re not going to get anything. If they did, they’ll get again 200 millilitres.”
They are never given more than one litre, twice a day. Otherwise, they will rush the bowl rather than going to the sow.
By the eighth day, the piglets are starting the switch to creep feed, so they get 500 ml of milk in the morning and then some creep feed is dumped in during the afternoon.
“We do that for two or three days in a row to make them get used to both, and then they are switched to the creep feed.”
Spruit is currently experimenting with bringing the gilts into the farrowing unit a few days earlier, and then providing them with some oral medication to help them relax and get them eating well in preparation for their first litter.
Early results indicate that the gilts are less stressed, eating better and giving more milk at farrowing time.
Spruit said the biggest takeaway from his story is to try to wean 85 to 90 per cent of piglets on the sow.
“That is the most important change that we’ve made in order to reduce our mortality.”
Keeping the smaller pigs with the sow and providing supplemental milk gives them an opportunity to thrive, while timely vaccination will improve their chances, he said.
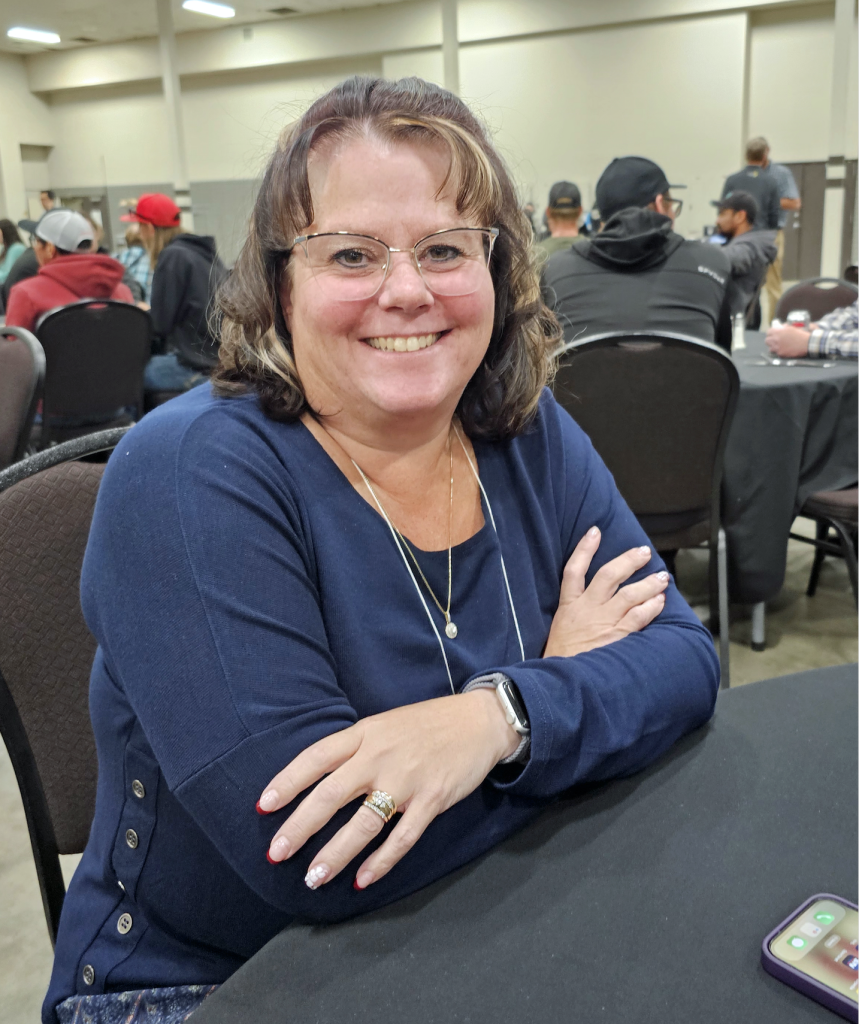
THE BOTTOM LINE ON HIRING TEMPORARY FOREIGN WORKERS
Trish Hyshka, human resources manager for Sunterra Farms, spoke of the advantages and challenges in hiring temporary foreign workers (TFW).
“The first thing we fight is public perception, and this is one of the things I struggle with the most,” Hyshka said, addressing an audience that included many people who had come from other countries to work on Canadian farms.
Those perceptions include beliefs that TFWs are little more than slaves, hired as cheap labour to save money for the farm.
“This is a huge frustration for the employer, that this is how the public sees the program,” said Hyshka.
Attempting to set the record straight, she said it would be much cheaper and easier to hire Canadians, if there were Canadians available and if they were willing to do the work.
“In general, Canadians don’t like to get their hands dirty or work really hard, If we are able to recruit Canadians, the turnover does become higher because we can’t compete with other industry wages in construction, oil and gas, etcetera,” she said.
The up-front costs of setting TFWs up in Canada adds up to an average of about $5,000, including travel, setting them up with groceries and subsidizing their housing costs. For companies like Sunterra Farms, it’s worth it, said Hyshka.
“It’s not the easy route, recruiting and hiring TFW’s. It takes a lot more work and administration. We deal with a government that wants to make it difficult for the employer to hire and retain TFWs. There are way more rules and regulations with the TFW program than there are if we just hire Canadians.”
Canadian employers face myriad challenges when they seek to hire help from other countries, the first of those being language, she said.
“We have many different languages on one team. This can lead to miscommunication and challenges with training and getting people up to speed generally.
“And of course, they want to speak their own language, but that divides the team and leaves people out of conversations, so this is something that we try to push, that when we’re all together, that we all speak English.”
With that, good English is necessary for anyone who wants to work up to a supervisory position, said Hyshka.
Next is the need for a driver’s licence. Working in rural locations in Western Canada can be especially lonely for people who already miss their family and friends. They need to be able to visit friends, go shopping, celebrate Christmas, those sorts of things.
“They’re living in the middle of nowhere. What can we do to make them not so lonely and homesick? We’ve had several people have to go home because they just get so homesick, and frankly, I would be one of those people,” said Hyshka.
Next up among challenges is the ever-evolving morass of regulations the federal government sets out for employers seeking TFWs, coupled with processing times that seem to get longer. The processing time currently stands at 128 business days – just over four months.
“Constant changing of the program and the requirements is a huge challenge,” says Hyshka.
“Each time we do an application . . . the rules have changed slightly, so this causes some delays if we’re not on top of the changes.
“For example, when they decided that education had to be evaluated by an equivalency agency to make sure it matched the Canadian GED (General Education Development) requirements at a minimum, this was extremely difficult for those TFW’s that have been away for school for several years, as you can imagine.
“In Mexico, for instance, if you’ve been out of school for 10 years and all of a sudden you need your transcripts to be specifically sent to an agency sealed from that institution, how do you get that organized?”
Vacation time is also an issue for people who live far from home and hope to get four to six weeks of paid time off so they can go home to their families.
Further challenge is raised by recent policy that prevents visitors from applying for a work permit while they are in Canada. For example, family members who have come for a visit must return to their home country and apply if they wish to work in Canada. This delay again raises the spectre of homesickness and missing loved ones.
Employers can come under investigation if a worker lodges a complaint with Service Canada in order to obtain an open work permit.
“Anybody that’s gone through an investigation with Service Canada knows how cumbersome it can be. Even if there’s no merit to the complaint, the employee gets an open work permit and the employer can do nothing. It’s very time consuming and very costly.”
Employer applications can also be subject to random investigations of their applications for workers. Hyshka said she wishes she has as much luck with lottery tickets as she has had with being selected for investigation.
Each investigation involves about 500 pages of paperwork, including proof that each cheque came out of the bank account, all time sheets, cheques and electronic funds transfers has to match. A non-compliance investigation can be launched if someone makes a complaint or if there is suspicion that the employer is not following the rules.
“Non-compliance can lead to fines, suspensions or termination from the TFW program. We do our very best to make sure there’s no merit to any complaints that gets submitted. We can’t stop the complaints, but we can make sure that we don’t have anything to worry about,” said Hyshka.
“The bottom line is, without the TFW program, we would not be in business. These people actually support our business. They work hard and they’re very loyal and dedicated to our company.”
Workshop participants also heard updates on loose housing of sows from Matt Davis of Hord Farms in Ohio, followed by a tag team discussion on converting to loose housing by Dave Tschetter from Holt Colony and Bryan Possberg from Blue Sky.
Nutritionists Malachy Young and Danilo Sotto provided advice for producers milling their own feeds, and Yolande Seddon, NSERC industrial research chair in swine welfare, gave an update on research projects at the Prairie Swine Centre. •
— By Brenda Kossowan