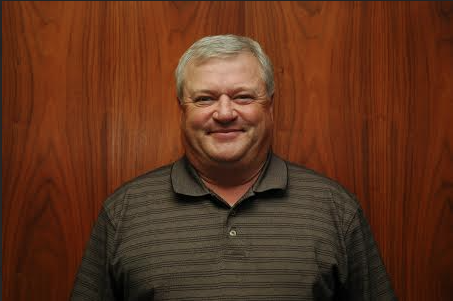
Project leader Murray Roeske, working on behalf of Alberta Pork and the ALMA (Alberta Livestock and Meat Agency), now has three years of data from those farms and offered his analysis of those results during Red Deer Swine Tech on Nov. 5.
Among his key findings is a determination that Alberta producers lose money when they ship pigs to the United States to be finished. He compared the data he had collected with reports from Meta Farms Inc., noting that some adjustments had to be made to account for weaning ages and market weights.
“We found out that we can actually finish pigs in the province of Alberta 13 days, 14 days faster than the US, and there’s also a $10-plus savings on that as well,” said Roeske.
“The question is why do we send hundreds of thousands of pigs from Alberta to the US to be finished? Alberta Pork, in collaboration with the competitive branch of ARD (Alberta Agriculture and Rural Development) are investigating why these animals are moving south to be finished.”
There are multiple factors, but as far as basic pig production is concerned, the finishing barns in Alberta are doing far better than their counterparts in Iowa, he said.
Overall, some factors cannot be controlled, said Roeske. The cost of production benchmark project offers Alberta producers some tools for managing the factors that are within their control, he said.
“The cost of production benchmark can help you manage revenues earned, feed utilization and purchasing.
“Alberta Pork and ALMA engaged in the project to sustain the competitiveness of the Alberta pork producers. Our key competitors are not necessarily our neighbours, but pork producers in Denmark, US, Brazil and China.
“Right now, as we speak, the product that we used to sell in Russia is being replaced by product coming out of China.”
There is an assumption that much of that product is being produced and exported through the back door in the United States by the Smithfield organization, which is now owned by the Chinese.
Looking more closely at variances on the 22 farms in the benchmarking project, Roeske said that, while the profit picture has improved dramatically, only two of the farms involved in the project actually made money in 2012, showing profits ranging from 39 cents to $5.88 per pig for that year.
There was a $54.59 difference per pig in feed costs on the 22 farms while there was a variance of $22.25 per pig on the revenue side. Those who got the consistently higher prices for their pigs were doing a better job of hitting the grids and were also using forward contracting to market their animals, said Roeske.
Factors in lower feed costs included weaning age, feed purchasing practices, use of a grain broker for timely delivery and quality control, use of local protein sources and feed conversion, he said.
The best feed conversion was coming from lower stocking densities, pre-selection of animals going into finishing so smaller animals were separated out, and strict monitoring of shipping weights.
A feed trial on one of the colonies determined that feed conversion drops off on bigger animals. Carrying heavy pigs loses on the index and on the feed conversion as compared with smaller pigs, he said.
“We talked to the two most profitable producers in 2011 and 2012, and what we found in 2011 and 2012 was, the guys who had the lowest feed costs actually generated profit (those years). With the pricing in that year, with the feed costs being the way they are, the thing to really close in on was feed.”
Addressing the value of benchmarking, Roeske said producers who took part in the project did not know how they stacked up against their fellow producers.
“Analysis of their COP allows us to discover variances that producers can use in making management decisions,” said Roeske. •
— By Brenda Kossowan